10 Shear Loading in Beams
Introduction
Click to expand
In Chapter 9 we learned how to calculate bending stresses in beams and how to design beams to resist bending stress. Transverse loading applied to beams will also create internal shear loads and therefore shear stresses that must be calculated and accounted for (Figure 10.1).
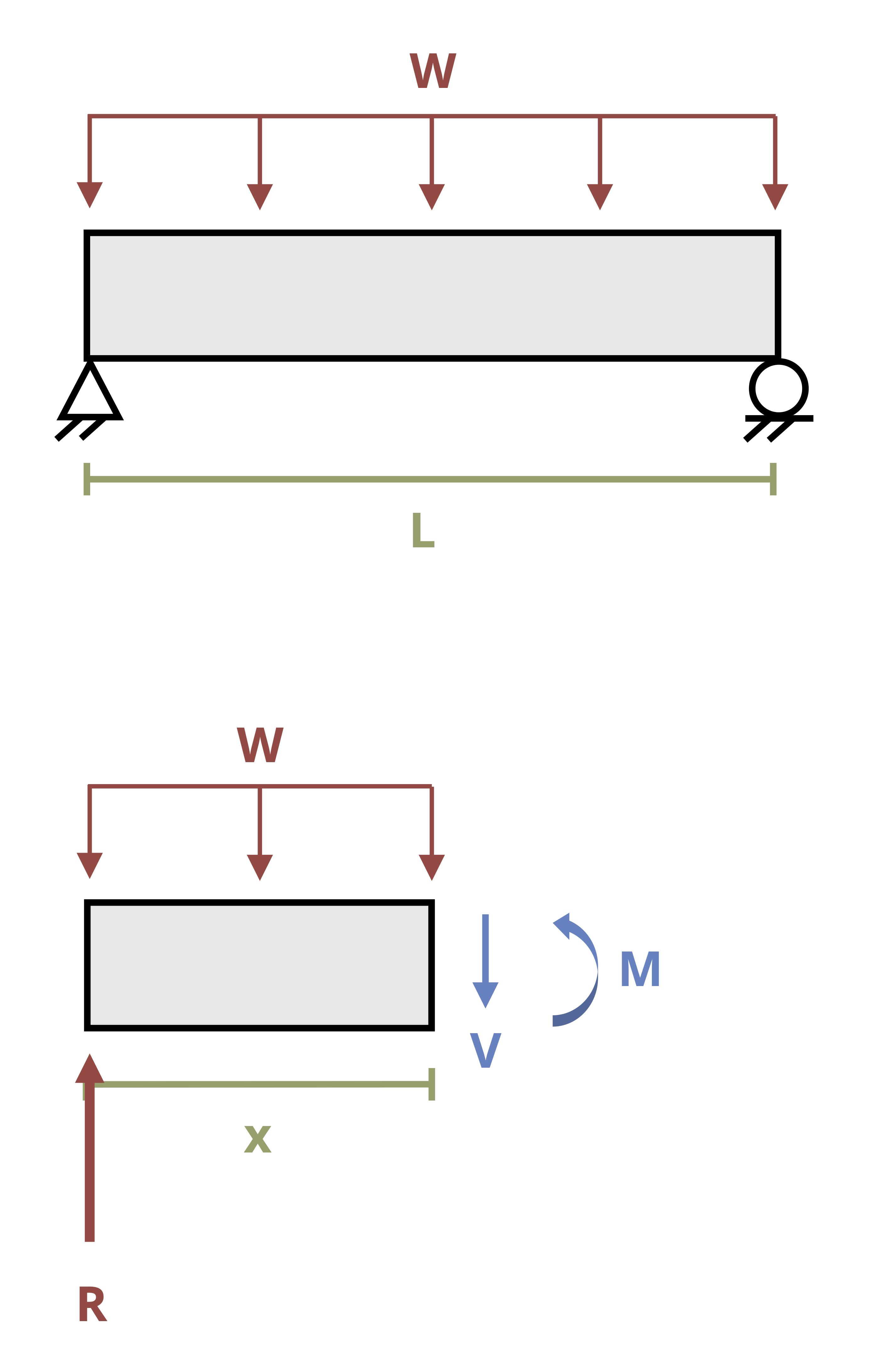
In this chapter, we’ll first review an important geometric property known as the first moment of area and demonstrate how to calculate it for common beam cross-sections in Section 10.1. In Section 10.2 we’ll discuss transverse shear stresses in beams and how to calculate them. In Section 10.3 we’ll discuss shear flow, which is useful for beams with cross-sections formed by joining two or more parts with fasteners such as nails.
10.1 The First Moment of Area
Click to expand
Shear stress in an object depends on the internal shear force and the shape of the cross-section. One important geometric property used in this chapter is the first moment of area. This property was introduced in Section 8.1 and was used when determining the centroid of an area. Recall we used Equation 8.1 to break simple cross-sections down into a number of composite parts. When finding the centroid of these composite areas we modified the equation slightly to:
\[ \bar{y}=\frac{\sum y_i A_i}{\sum A_i}=\frac{y_1 A_1+y_2 A_2+\ldots}{A_1+A_2+\ldots} \]
We can rewrite this equation in its integral form:
\[ \bar{y}=\frac{\int y d A}{\int d A} \]
The numerator in this equation is the first moment of area. It will be given the symbol Q.
\[ Q=\int y d A \]
Similarly, for the purposes of this text we can write:
\[ \boxed{Q=\sum y_i A_i=y_1 A_1+y_2 A_2+\ldots} \tag{10.1}\]
Q = First moment of area [m3, in.3]
y = Vertical distance from neutral axis to centroid of area A [m, in.]
A = Area above (or below) point of interest [m2, in.2]
In Section 8.1 we performed this calculation relative to some convenient reference axis in order to determine the location of the centroid of an area (such as in Example 8.3). Ai represents the area of each composite part and yi represents the distance from the reference axis to the centroid of each composite part.
The first moment of area can actually be calculated around any axis. The maximum value will always occur at the centroid of the cross-section (i.e. the neutral axis for pure bending) so many problems will involve finding the first moment of area at the neutral axis, but there are also cases where finding the first moment of area around some other axis is required. Note that the axis should be perpendicular to the shear force, so a vertical load requires us to use a horizontal axis.
To calculate the first moment of area around an axis, first draw a line through this axis. We may choose to use either the area above this axis or the area below it, whichever is simpler. The answer will be the same either way. Break this area down into composite parts (if necessary) and apply \(Q=\sum y_i A_i\) where Ai is the area of each composite part and yi is the perpendicular distance between the centroid of the overall cross-section and the centroid of each composite part. Note that we must first find the location of the centroid of the overall cross-section in order to measure this distance. Figure 10.2 illustrates this process for finding Q at the neutral axis and at another axis for two different cross-sections.
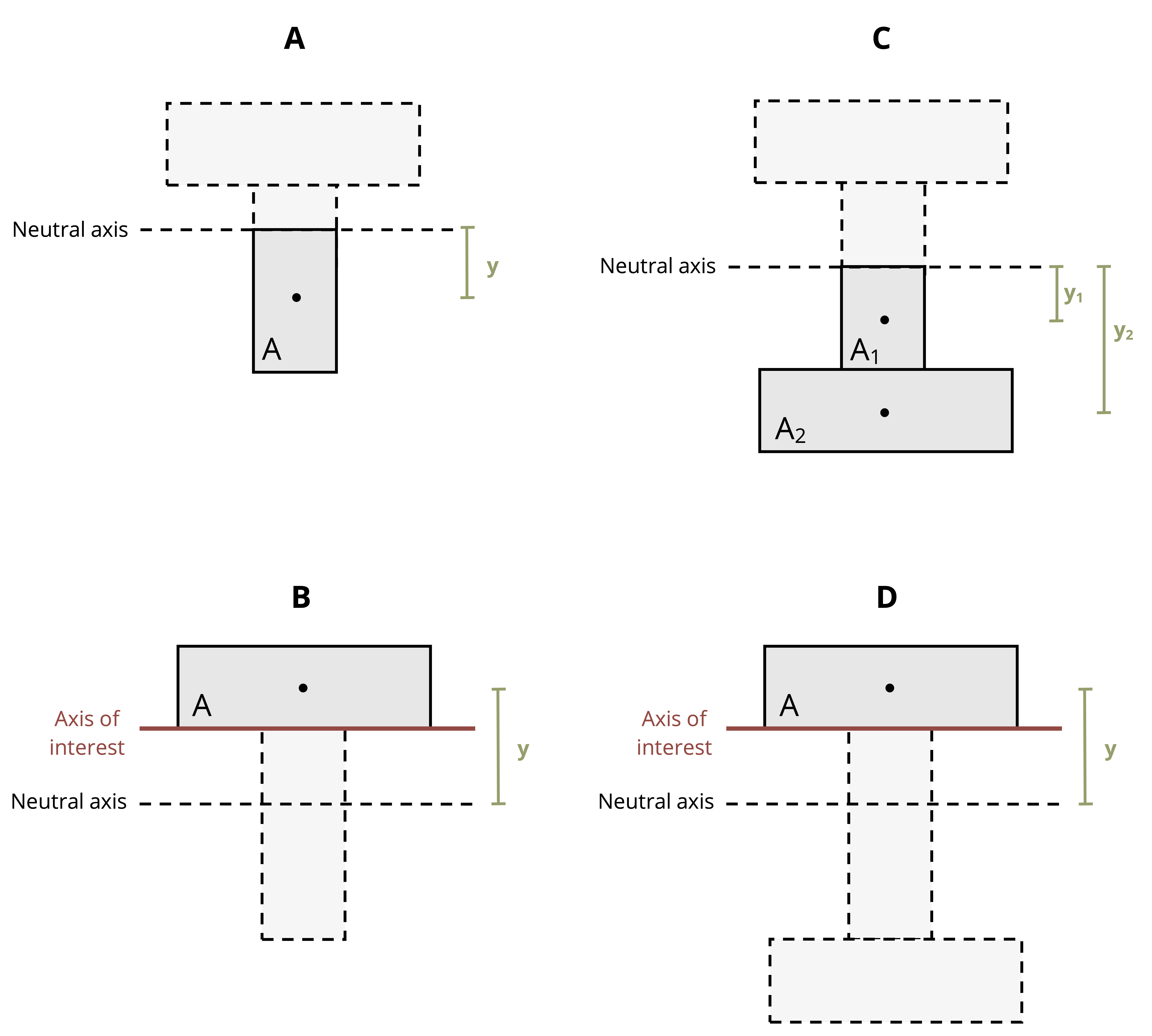
Example 10.1 demonstrates this process to find the first moment of area around the neutral axis of a T cross-section. This example is solved twice, once using the area below the neutral axis and once using the area above.
Example 10.2 uses the same cross-section and demonstrates calculating the first moment of area around a different axis on the cross-section.
Simple cross-sections such as rectangles and circles are fairly commonly used for beams. For these simple cross-sections we can derive standard solutions for the maximum first moment of area (Qmax). Recall that this always occurs at the neutral axis of the cross-section.
For a rectangle of base b and height h (Figure 10.3), the neutral axis will be at \(y=\frac{h}{2}\). Drawing a line along the neutral axis and taking the area above this line gives \(A=b \frac{h}{2}\). The distance between the centroid of this area and the neutral axis of the cross-section will be \(y=\frac{h}{4}\). Thus, for a rectangular cross-section:
\[ Q_{\max }=\frac{h}{4} \frac{b h}{2}=\frac{b h^2}{8} \]
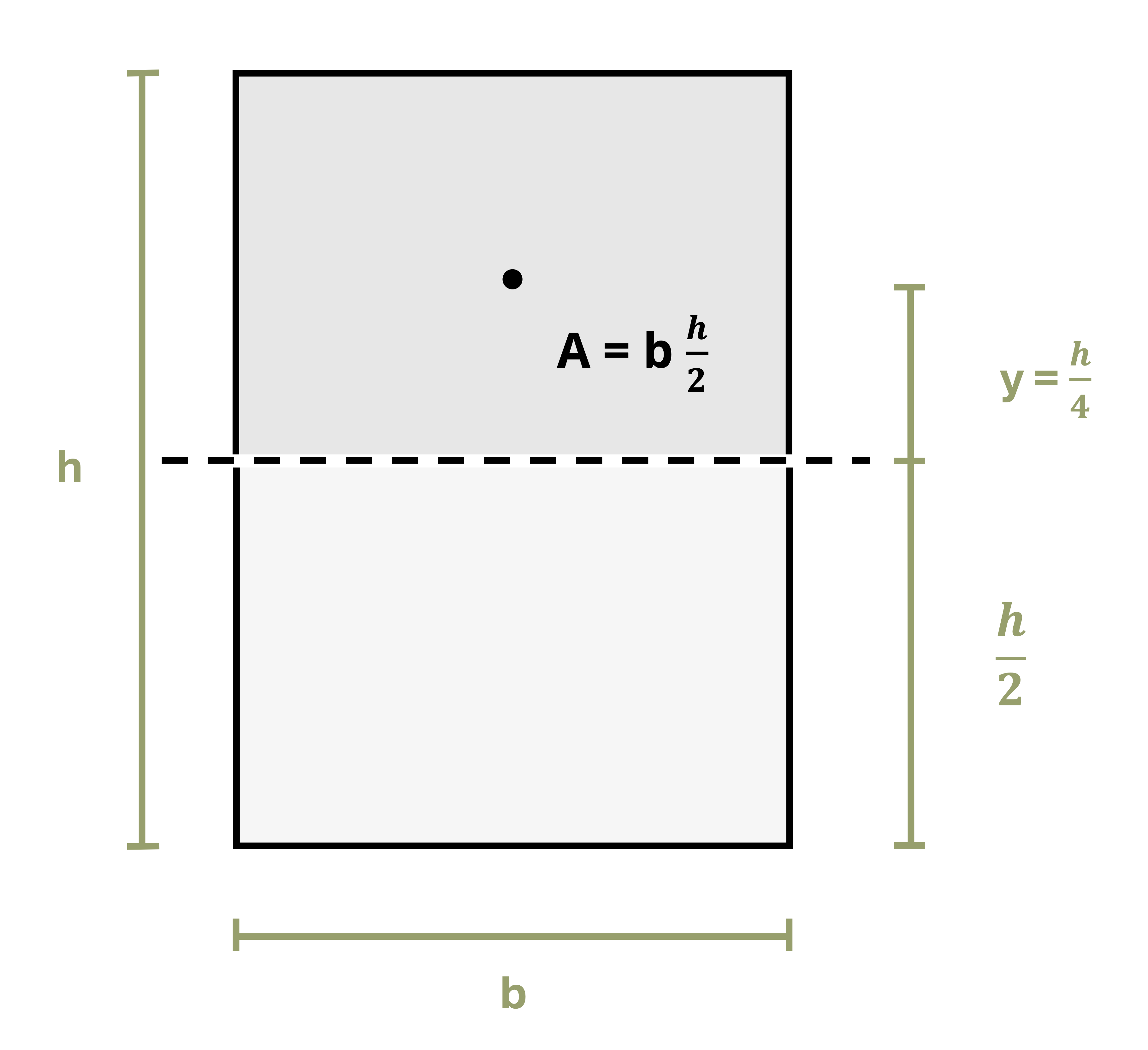
For a circular cross-section of radius r (Figure 10.4), the area above the neutral axis is semi-circle so \(A=\frac{1}{2} \pi r^2\). The distance from the centroid of the semi-circle to the neutral axis is \(y=\frac{4 r}{3 \pi}\). Thus, for a circular cross-section:
\[ Q_{\max }=\frac{4 r}{3 \pi} \frac{1}{2} \pi r^2=\frac{2}{3} r^3 \]
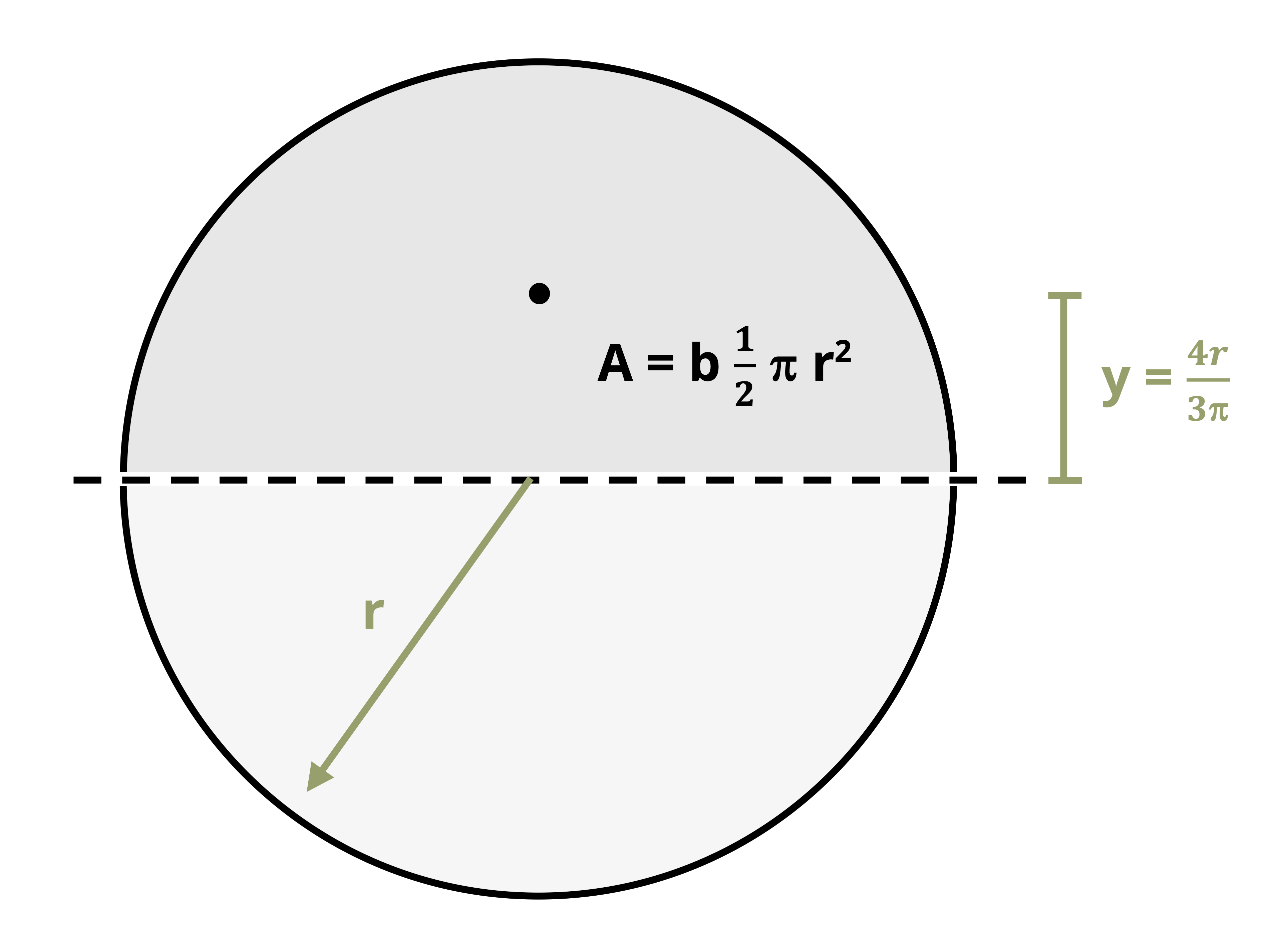
Note that both of these are only for finding the first moment of area at the neutral axis (Qmax). If the first moment of area around any other axis is required, these shortcuts will not work, and the general process will need to be used.
10.2 Shear Stress
Click to expand
In Section 2.2 we learned about average shear stress:
\[ \tau_{avg}=\frac{V}{A} \]
This is the average shear stress on a cross-section, but shear stress actually varies through the height of the section (Figure 10.5). For a vertical internal shear force, the shear stress is zero at the top and bottom of a cross-section and maximum at the neutral axis. Shear stress varies in a parabolic fashion. The average shear stress does not provide a full picture and it is often necessary to calculate the shear stress at a specific point on the cross-section instead.
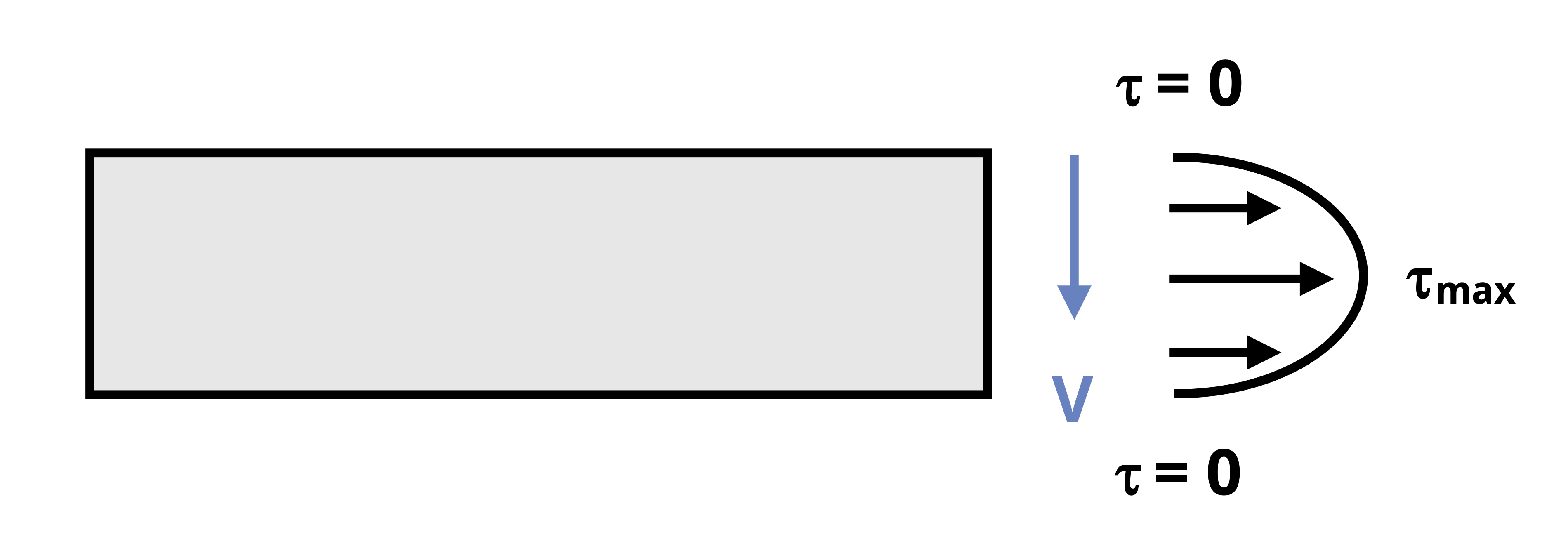
To derive the shear stress formula, we’ll begin by examining a small 2D element on a body subjected to an internal shear force (Figure 10.6). If this element is in equilibrium, a shear force applied to one face of this element must also produce shear forces (and therefore shear stresses) on the other faces of the element.
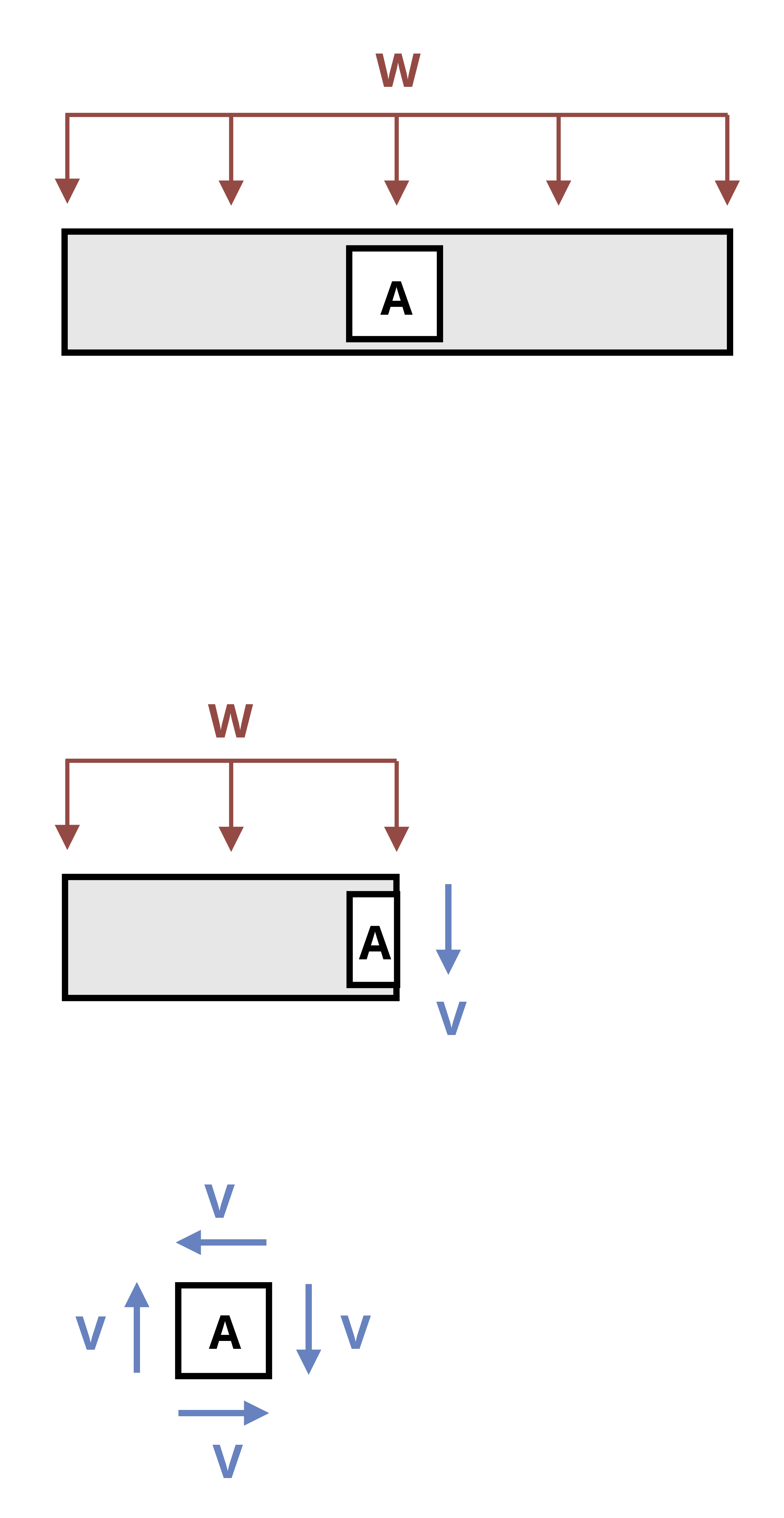
Thus, an element experiencing a vertical shear stress also experiences a horizontal shear stress. This is known as the complementary property of shear. This effect can be seen by forming a ‘beam’ out of a stack of paper and applying a vertical force. The pieces of paper slide horizontally relative to each other (Figure 10.7).
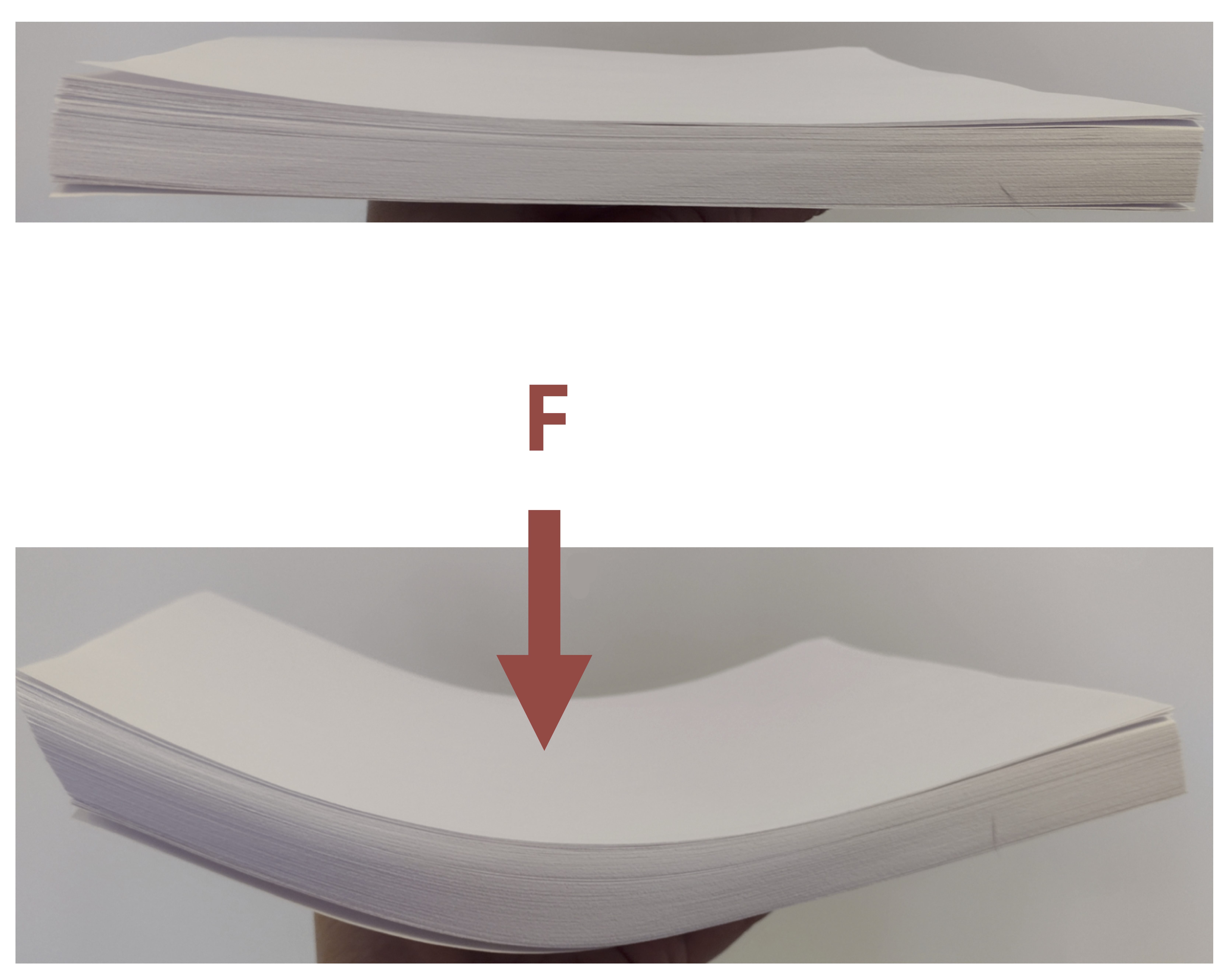
Another example is a wooden beam that fails due to transverse shear. In such beams, cracks tend to appear horizontally even though the applied load is vertical. This is due to horizontal shear stress between the layers of the wood (Figure 10.8).
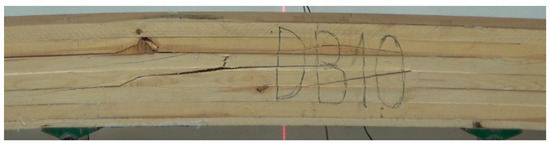
Imagine a beam subjected to an arbitrary vertical load. Consider a small cross-section of width Δx (Figure 10.9). This cross-section is subjected to an external load, an internal shear force on each side of the cross-section, and an internal bending moment on each side of the cross-section. The two shear forces and two bending moments are not necessarily equal.
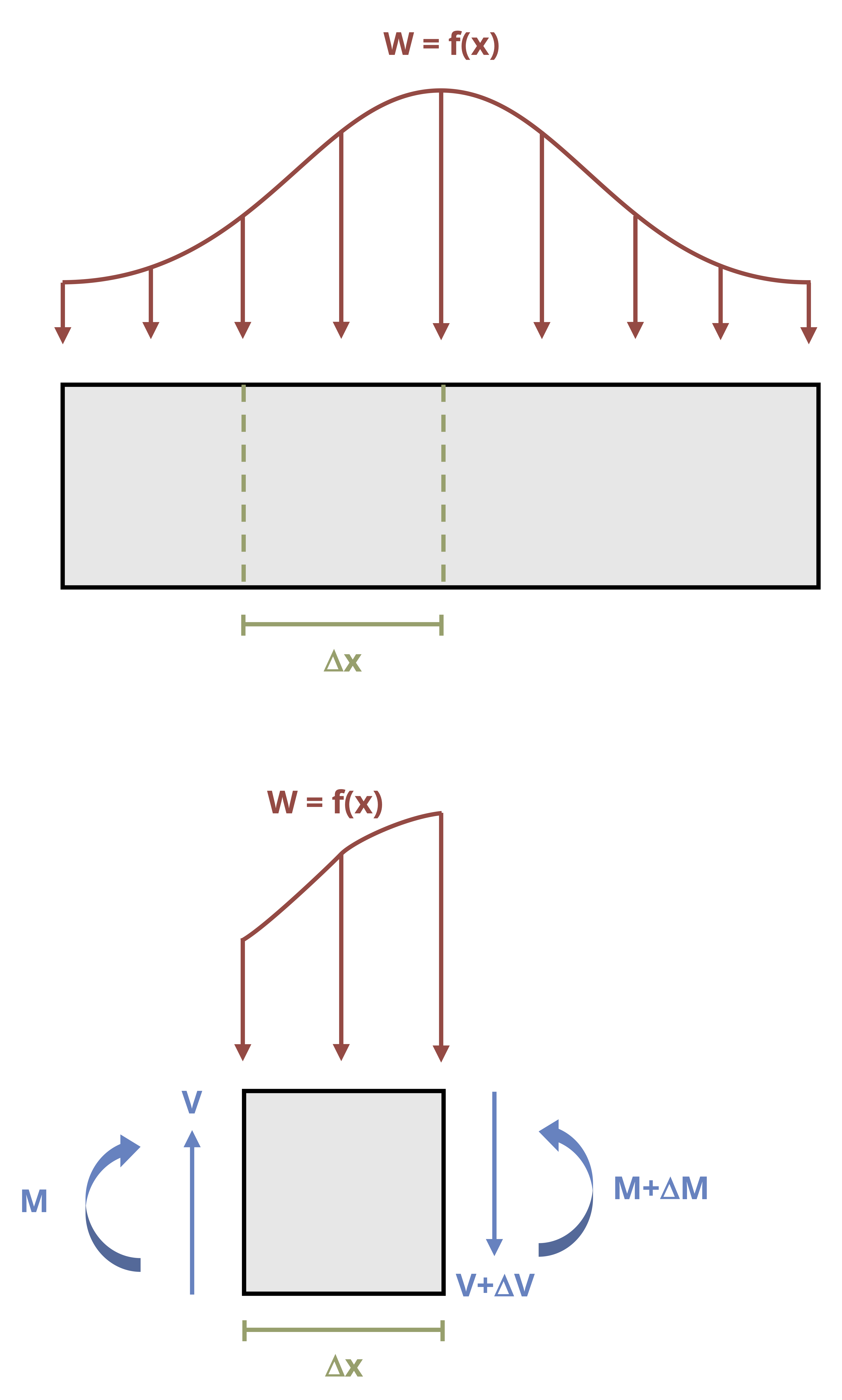
By considering horizontal equilibrium, we do not need to account for the vertical loads (V, V + ΔV, and w). From the flexure formula (Equation 9.2) the bending moments (M and M + ΔM) will create horizontal stresses (Figure 10.10) equal to
\[ \sigma_{x 1}=\frac{M y}{I} \]
and
\[ \sigma_{x 2}=\frac{(M+\Delta M) y}{I} \]
Since \(F=\sigma A\), we can determine the total force applied by each bending moment:
\[ F_1=\int \frac{M y}{I} d A \]
and
\[ F_2=\int \frac{(M+\Delta M) y}{I} d A \]
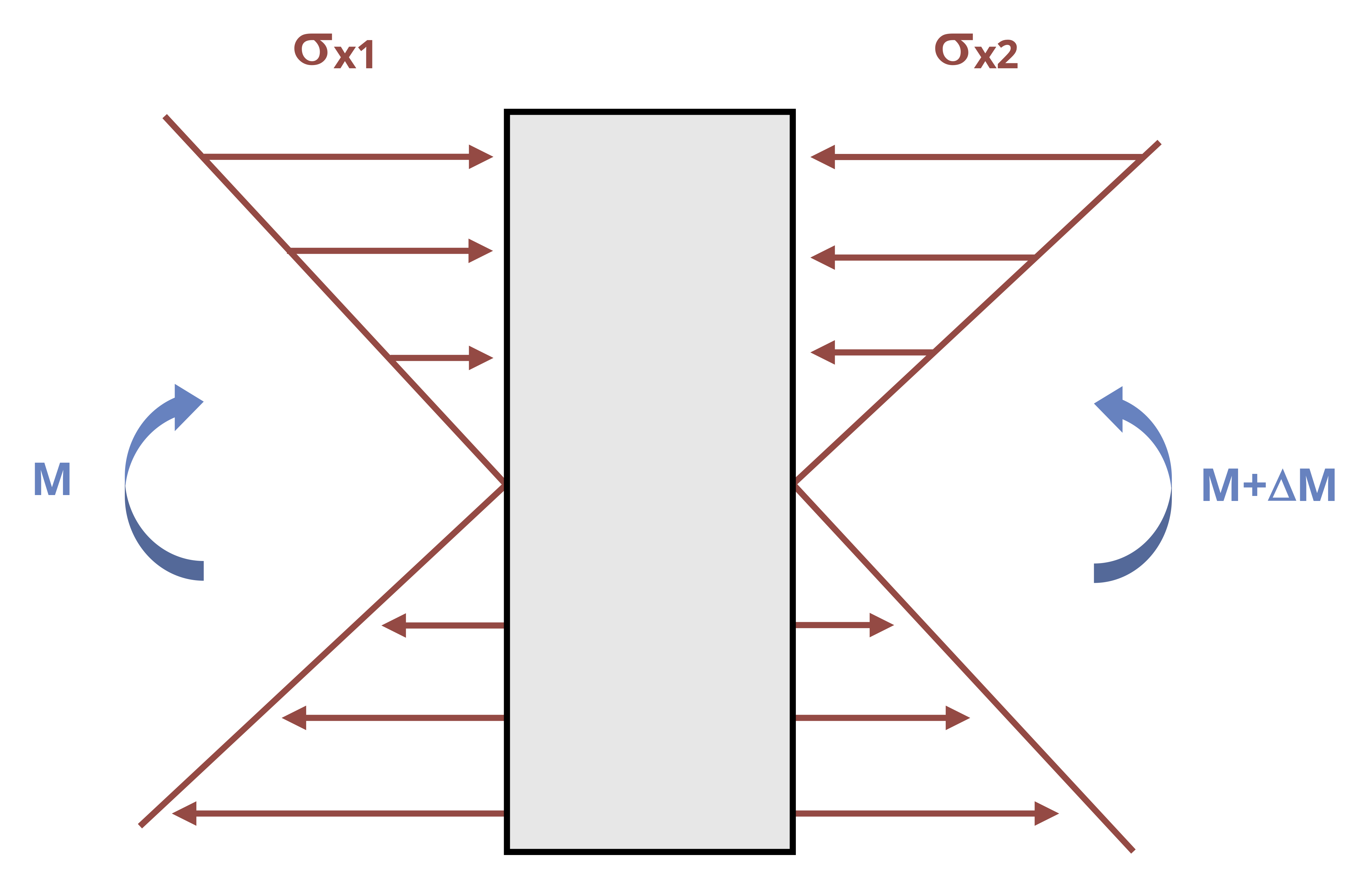
Each force is tensile in part of the beam and compressive in part of the beam. When calculated across the entire cross-section these forces will sum to zero. However, if we consider only part of the cross-section the forces do not sum to zero (Figure 10.11). For the beam to be in equilibrium, there must be a horizontal shear force. For now, we’ll call this force F’ and derive an equation for the shear stress it creates.
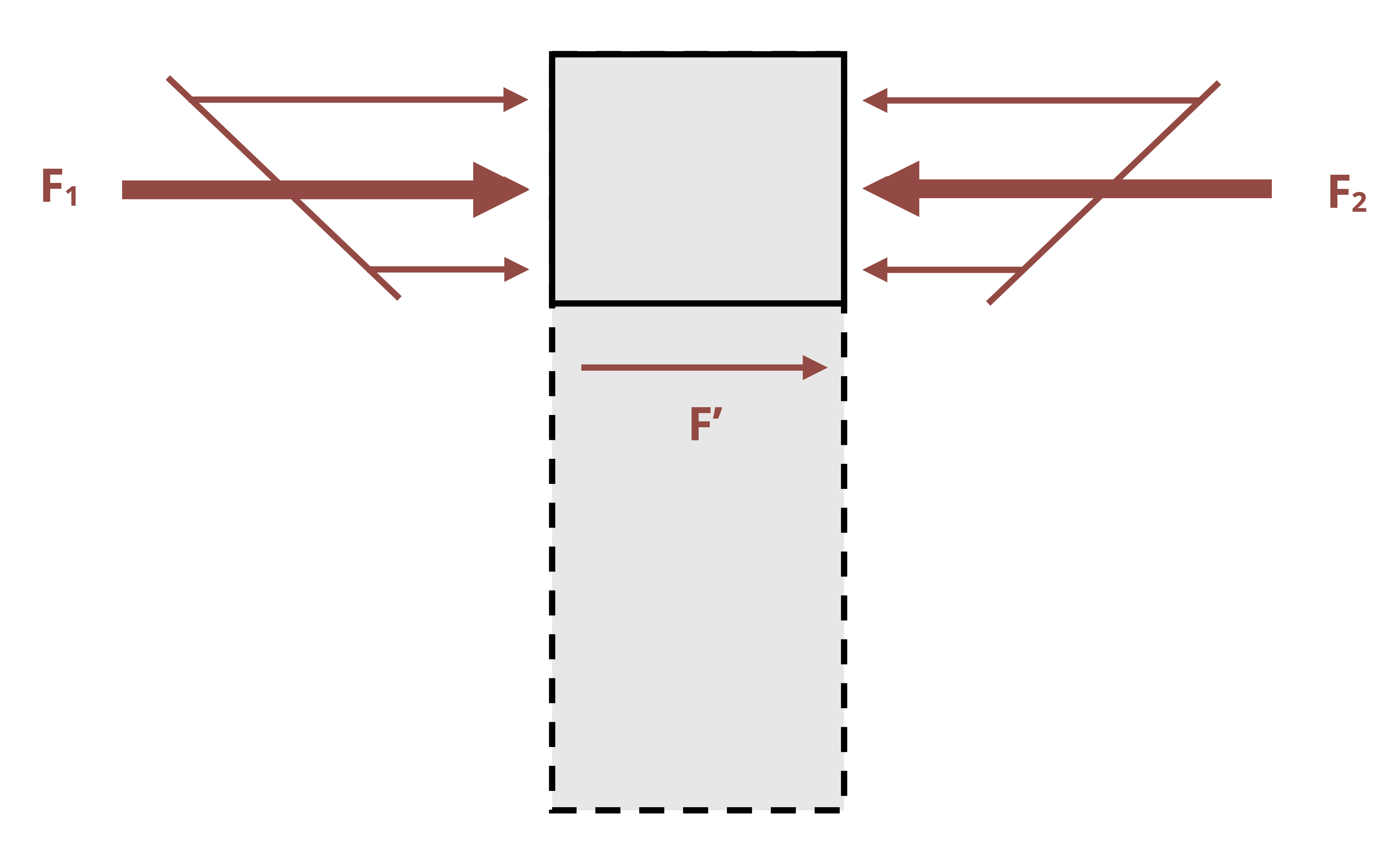
By equilibrium:
\[ \begin{aligned} & \sum F_x=F^{\prime}+\int \frac{M y}{I} d A-\int \frac{(M+\Delta M) y}{I} d A=0 \\ & F^{\prime}=-\int \frac{M y}{I} d A+\int \frac{M y}{I} d A+\int \frac{\Delta M y}{I} d A \\ & F^{\prime}=\int \frac{\Delta M y}{I} d A=\frac{\Delta M}{I} \int y d A \end{aligned} \]
Once the constants are taken out of the integral, the remaining integral is just the first moment of area, Q.
\[ F^{\prime}=\frac{\Delta M}{I} Q \]
We can calculate the transverse shear stress from \(\tau=\frac{V}{A}\) where V = F’ and A is the area of the cross-section that force F’ acts on. This area will be width, Δx, multiplied by the thickness of the beam, t.
\[ \tau=\frac{V}{A}=\frac{F^{\prime}}{\Delta x t}=\frac{\Delta M Q}{\Delta x I t} \]
From Section 7.2 we know that the change in moment with respect to x is equal to the shear force, V
\[ \frac{\Delta M}{\Delta x}=V \\ \]
\[ \boxed{\tau=\frac{VQ}{It}} \tag{10.2}\]
τ = Transverse shear stress at a point on the cross-section [Pa, psi]
V = Internal shear force at the cross-section [N, lb]
Q = 1st moment of area at the point of interest on the cross-section [m3, in.3]
I = Area moment of inertia of the cross-section [m4, in.4]
t = thickness of the cross-section [m, in.]
This is the transverse shear stress equation, allowing us to calculate the transverse shear stress at any point on a cross-section. This is often more useful than simply calculating the average shear stress across the entire cross-section.
Example 10.3 demonstrates calculation of the maximum transverse shear stress in a simply supported beam with a circular cross-section.
Note that the first moment of area will always be at its maximum value at the neutral axis of the cross-section. Since shear stress, \(\tau=\frac{VQ}{It}\), the maximum shear stress often occurs at the neutral axis too. This will be true if the thickness, t, of the cross-section is uniform (such as a rectangular cross-section) or at its thinnest at the neutral axis (such as a wide-flange beam). However, if thickness t is larger at the neutral axis than at another point in the beam, it is possible that the maximum shear stress will occur at the point where the thickness decreases even though Q will be smaller at this location than at the neutral axis. In these cases it is best to calculate the shear stress at both the neutral axis and at the location where the thickness decreases. Example 10.4 demonstrates how to calculate the maximum transverse stress is a cross-section of varying thickness.
10.3 Shear Flow
Click to expand
Some cross-sections are formed by connecting multiple pieces together with fasteners such as nails or bolts (Figure 10.12). In such members, we must analyze not only the stresses in the cross-section itself but also the stresses in the fasteners.
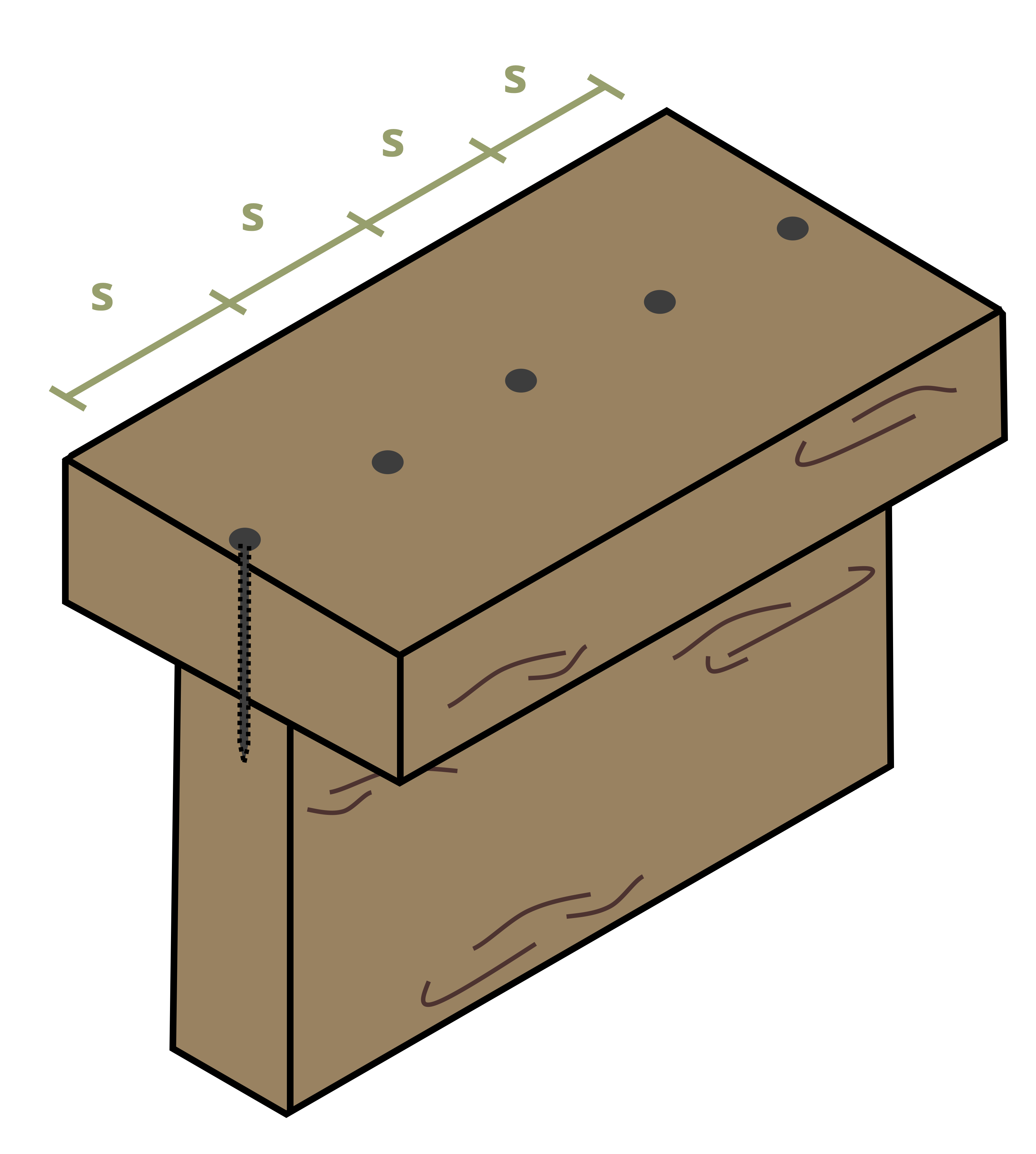
A useful quantity in this regard is shear flow, q. Shear flow measures of how much shear force is applied per unit length of the beam, and it is measured in units of force/length [N/m, lb/in.]. For example, if a nail is capable of resisting a shear force up to 10 kN and there is a shear flow of 30 kN/m, it is trivial to determine that we need at least 3 nails for every meter of beam.
Recall from Section 10.2 that the internal horizontal shear force, F’, may be written as
\[ F^{\prime}=\frac{\Delta M}{I} Q \]
Dividing both sides by Δx
\[ \frac{F^{\prime}}{\Delta x}=\frac{\Delta M Q}{\Delta x I} \]
Similar to our derivation in the previous section, we may replace \(\frac{\Delta M}{\Delta x}=V\). We may also replace \(\frac{F^{\prime}}{\Delta x}=q\).
\[ q=\frac{V Q}{I} \]
This equation is very similar to the shear stress equation, but the thickness of the cross-section doesn’t appear here as shear flow is measured per unit length. We will generally want to determine the shear flow at the seam where the individual pieces of the cross-section are joined together as this is where the fasteners must resist the horizontal shear force.
Often we want to determine how far apart we can space the nails along the length of the beam. Since shear flow is the shear force per unit length, if we know how much shear force each fastener can resist, we can say that the shear flow is equal to the force resisted by each fastener (Fnail) divided by the spacing between the fasteners (s). Sometimes there will be multiple rows of nails side-by-side (Figure 10.13). In this case we can multiply the force resisted by each fastener by the number of rows (r).
\[ \boxed{q=\frac{V Q}{I}=\frac{F_{nail} r}{s}} \tag{10.3}\]
q = Shear flow at a line on the cross-section [N/m, lb/in.]
V = Internal shear force at the cross-section [N, lb]
Q = 1st moment of area at the point of interest on the cross-section [m3, in.3]
I = Area moment of inertia of the cross-section [m4, in4]
Fnail = Horizontal shear force resisted by each nail [N, lb]
r = Number of rows of nails resisting the shear force
s = Spacing between nails [m, in.]
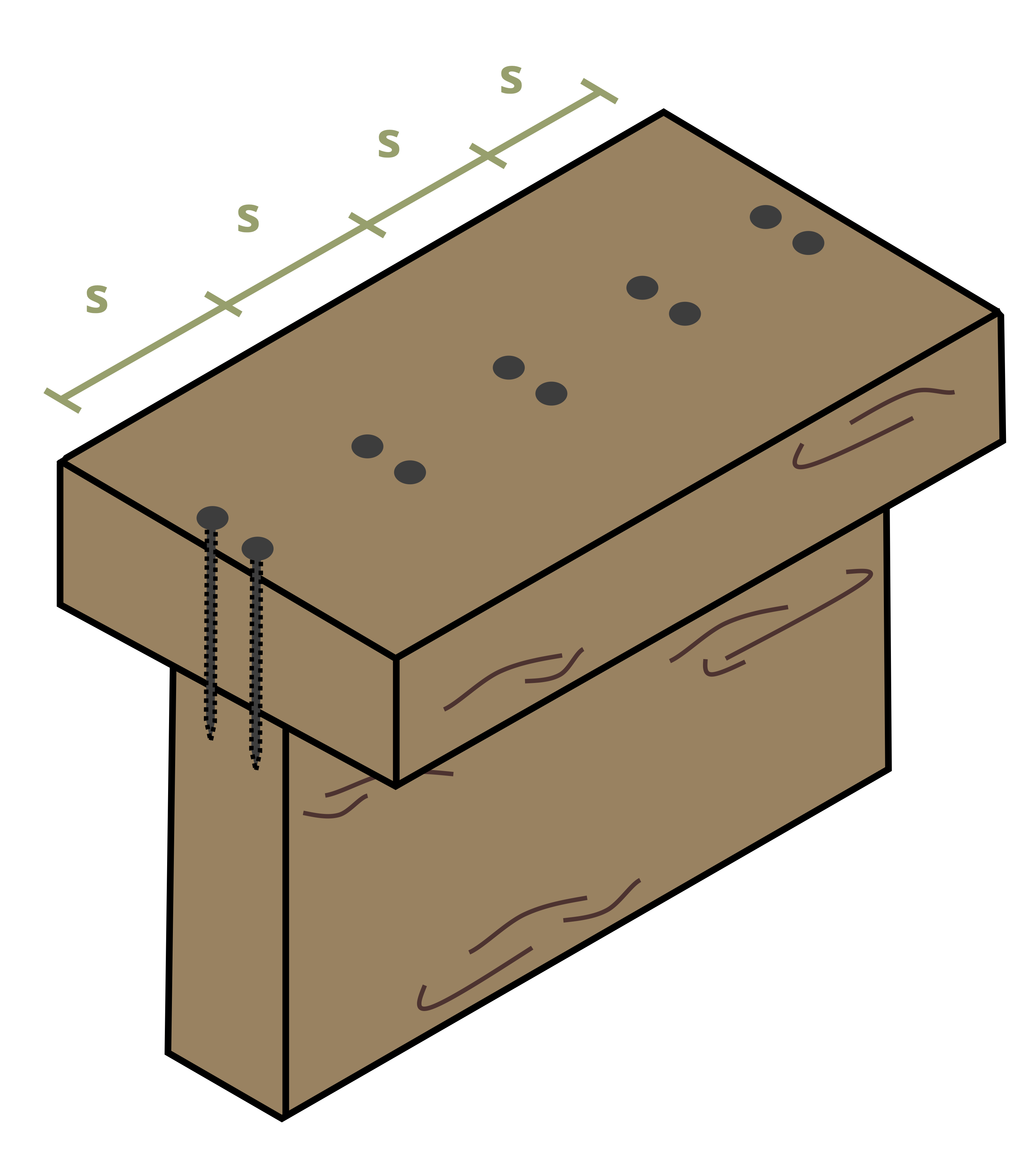
Sometimes fasteners may be placed horizontally (Figure 10.14). In these cases we should still draw a line along the seam perpendicular to the fastener (so vertically in this case). We can then use the area either to the left or right of this line to determine the first moment of area. Note that we still use the vertical distance between the centroid of our chosen area and the neutral axis of the cross-section. For cross-sections with an axis of symmetry, we may choose to draw one vertical line and use the area to the left (or right) of this line or we may draw two vertical lines, one at each seam, and use the area between (or outside of) these lines.
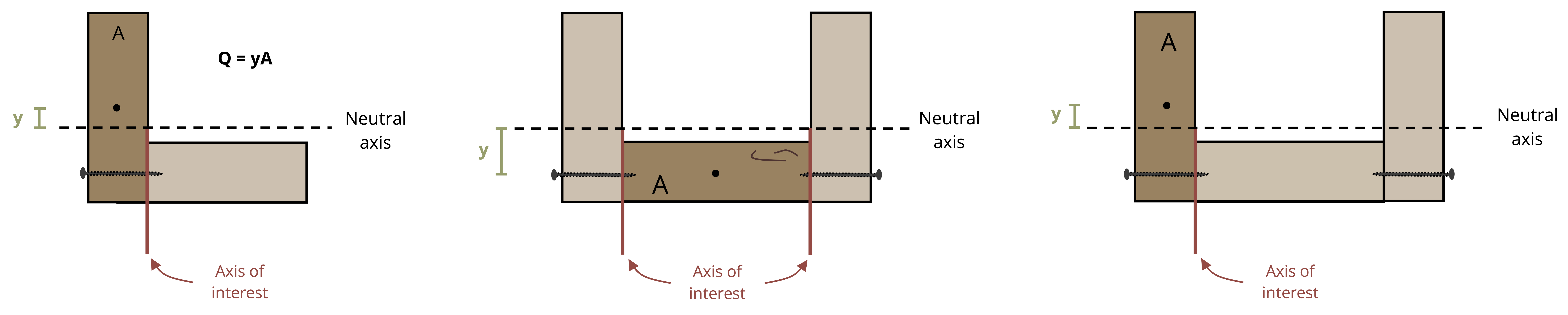
Example 10.5 works through a problem with two rows of nails at each seam.
Example 10.6 involves an L-beam with a horizontal nail.
Summary
Click to expand
References
Click to expand
Figures
All figures in this chapter were created by Kindred Grey in 2025 and released under a CC BY-NC-SA license, except for:
Figure 10.7: A stack of papers representing a beam. James Lord. 2024. CC BY-NC-SA.
Figure 10.8: Horizontal shear failure in a wooden beam subjected to a vertical load. Figure 8 in Adam Derkowski, Marcin Kuliński, Adrian Trociński, Jakub Kawalerczyk, and Radosław Mirski. 2022. Mechanical Characterization of Glued Laminated Beams Containing Selected Wood Species in the Tension Zone. Materials 15(18), 6380. https://doi.org/10.3390/ma15186380. CC BY 4.0.